Port slowdowns are still clogging up the nation’s supply chains, and it’s a big problem to solve. Ray Bowman is Director of the Small Business Development Center of Santa Barbara and Ventura counties in Southern California. He’s also the program chair for the District Export Council of Southern California. The business veteran and trade consultant said things have improved a bit but only on one side of the import-export equation.
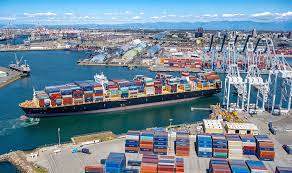
“Many things are going on to help with the port slowdowns,” he said on the phone from his office in Camarillo, California. “Most of us have seen the news footage of ships backed up and waiting to unload their cargo. A big part of the backup is the unprecedented buying demand we saw during COVID-19.”
He says the Biden administration moved to get the nation’s ports operating on a 24-hour basis or, at least, get that framework in place to help relieve congestion. Bowman says it’s helped somewhat on the import side of the business, where he says things are about 30 percent better than before.
“Unfortunately, I don’t see that it’s improved on the export side,” Bowman says. “So that’s been tough on American shippers who need to move their goods overseas.
“We knew there would be a significant increase in buying during COVID-19,” he said. “Up until recently, we haven’t seen much of a slowdown in purchasing. Companies are likely still trying to fill orders backlogged for months.”
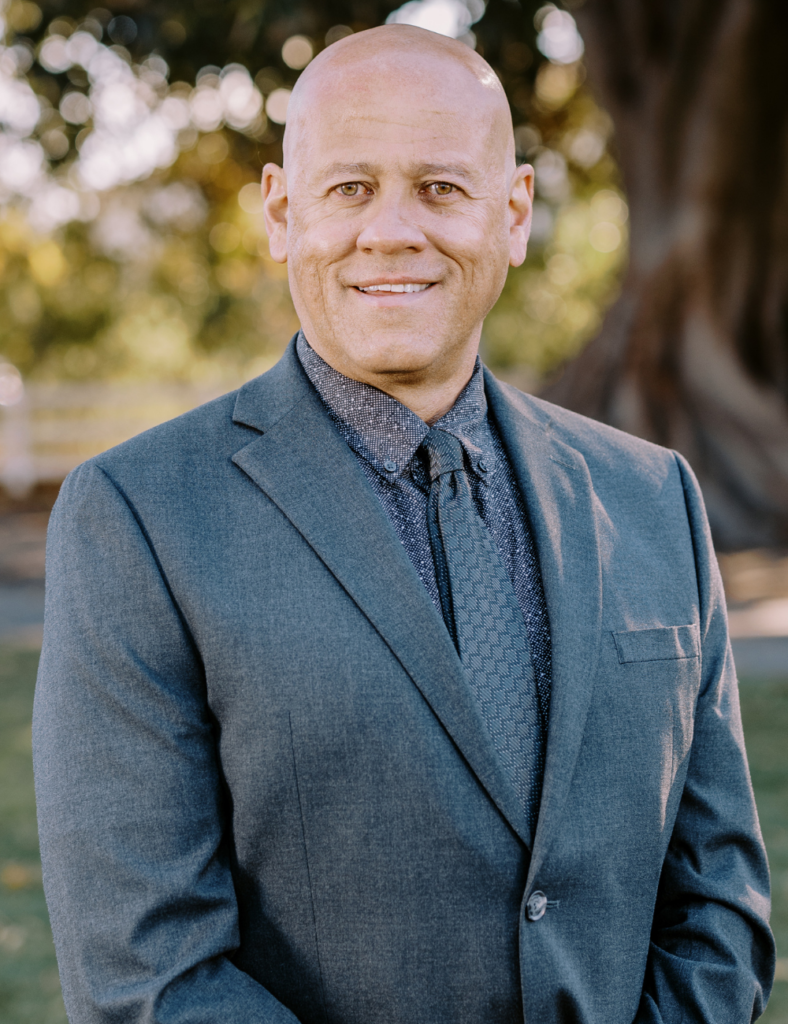
With so much demand for containers on the import side, it’s very difficult for shippers to simply find export containers to load their goods in. Companies started focusing more and more on the import side because they were making so much more money.
When it comes to export containers, fewer goods are leaving the country, so it tends to be cheaper to purchase export containers. They aren’t worth as much to the steamship lines as the larger volume of goods coming into the country. “Because of the demand for imports, steamship companies put all their space availability on the import side,” he said. “They didn’t pay as much attention to the export side, making containers much harder to find.
“The price of those containers is another limiting factor,” Bowman said. “As demand increased, the price shot higher at an unprecedented rate. We knew the price would increase because those costs have gotten suppressed in recent years, but we didn’t expect it to climb by ridiculously huge amounts.”
Limited amounts of containers and exorbitantly high prices hit the small and medium-sized companies harder than the larger businesses. He said the larger companies have economies of scale built into their business structures. Many typically have contracts for consistent shipping availability and trucking services regularly available.
“Small and medium companies buy their services primarily off the spot market,” Bowman said. “So, those higher prices hit those companies even harder than their larger competitors. These things like container shortages haven’t come out of the blue. This has been going on for some time, but when buying spikes as we’ve seen recently, there’s a point at which a system can’t efficiently handle the excess demand. That’s when we get significant port slowdowns.”
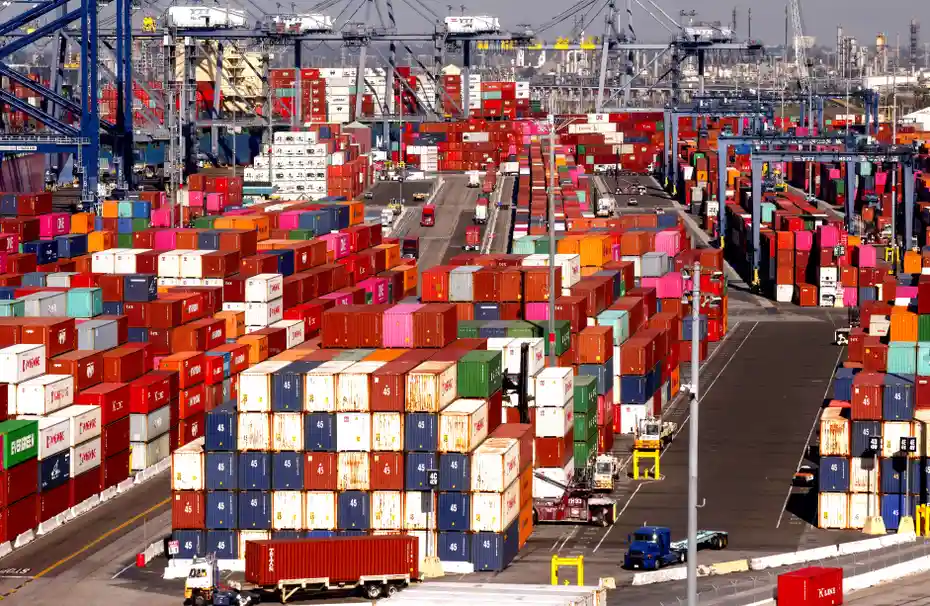
In addition to the small pool of available containers, Bowman said warehousing space for unloaded goods is almost maxed out. American warehousing only has roughly three percent of its total space available, which is not a good thing. He says the West Coast ports have less than two percent of space available.
“That only makes the container shortage worse because you have to be able to empty containers to make them available,” he said.
Many truckers who deliver to ports run into something called a “dual transaction” requirement. Bowman said that means if a trucker has a container to drop off, they’d better have another one to pick up. If a driver has a container to pick up, they’d better have another one to drop off. It’s efficient on paper, but if a driver doesn’t have that second part of the dual transaction, they’ll have to go find one.
“Another big challenge at the ports is something called the ‘Box Rule,’” he said. “When a trucker drops off a container to a particular shipping company, you have to have a chassis. Those are the wheels on the bottom that you load the container on.
“These steamship companies have contracts with different chassis makers,” Bowman said. “A steamship line will say, ‘if you’re going to tender one of our containers, you also have the chassis of the company we’ve contracted with.’ If you don’t have the right chassis to go with the right container, you’ll find yourself with cargo, the booking, and nowhere to unload it.”
Bowman, a business veteran with over 30 years of experience, says there is a lot of conversation about not having a Box Rule at the country’s ports. Shippers don’t want to worry about where the chassis comes from. Instead, they want the companies to bill whoever needs to get billed to use a chassis.
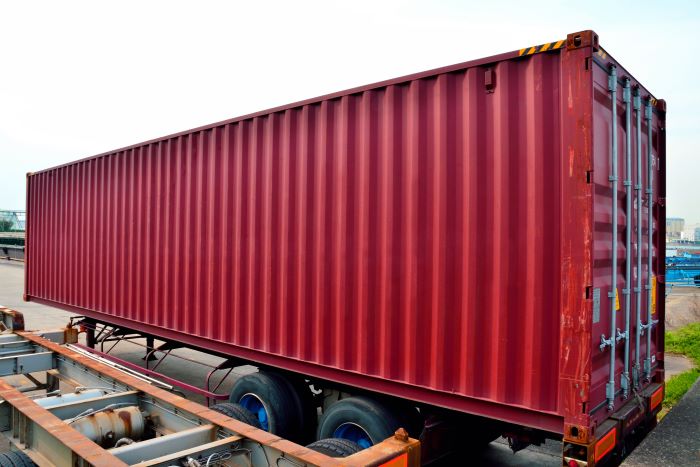
“Because of rules like this, roughly 30 percent of truck drivers miss their appointments,” Bowman said. “if you aren’t there on time for whatever reason, such as looking for a chassis, there’s no recourse. You’ve missed your appointment. It’s not unusual, at all, for a trucker to get there hours early and miss their appointment because they’re stuck in a queue.”
Another big reason that things get bogged down is a backlog. A lot of the shipments coming in right now got booked 90 days ago, if not longer.
While shippers, port officials, and government officials are looking at how to rectify these different challenges, Bowman says one of the biggest challenges is a lack of adequate infrastructure at the ports. Most of America’s ports were built when ships were typically much smaller than they are today.
“When I started in the shipping industry, a large ship was around a 4,000-container capacity,” he recalled. “In the 1980s, that was a big ship. Now, we have ships that can hold between 10,000 and 20,000 containers.
“Not only are they bigger, but these ships also just aren’t one carrier like they used to be,” Bowman added. “It used to be one carrier, one ship. You now have what are called ‘Shipping Alliances.’ In fact, there are three big ones in the U.S. As many as four or more steamship lines can be sharing space on one ship.”
Bowman said one of his biggest personal concerns is agricultural goods. If a shipment of consumer electronics takes a long time to get where it needs to go, the products aren’t in any danger of spoiling. Agricultural shipments contain perishable products that won’t wait long for a container and ship.
“A lot of attention needs to get paid to that,” he said. “Those are some of our best exports, and we need to protect that part of the supply chain.”
Bowman is an internationally-respected business consultant who says he’s never seen anything like this before. “There have been port slowdowns in the past, but this is truly unprecedented,” he said.